
Real-time component recognition in vehicle production - optimization with RFID!
Towing eye detected!
Component recognition in vehicle production - optimization with RFID
Another complex problem in the automotive industry that required a smart solution.
The task
A component in the vehicle MUST be verifiably built/installed in the vehicle. In this case it was the ASÖ (towing eye). According to legal requirements, this must be installed in the vehicle when it leaves the factory.
This check was currently carried out according to the 4-eyes principle. The installation was documented twice in writing on a control document. Nevertheless, it happened again and again that vehicles left the factory WITHOUT the ASÖ. In addition, a 4-eyes principle is complicated and expensive these days.
A solution was therefore sought that would automatically check and electronically document without human intervention. This is where RFID technology comes into play.
First, the ASÖ had to be tagged. The attachment of the tag requires several requirements in order to function sustainably. The OEM contacted us and asked RadioForce GmbH to develop a solution for this complex task.
Reading ability, reading range, building at the ASÖ, robustness and other features were the basic requirements for a working solution.
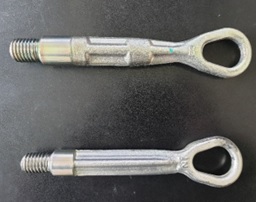
RFID gate with aligned antennas.
Other features were the installation in the vehicle, the right RFID antennas and readers, the installation of the antennas in the production line and the optimization of the process in the line.
Solution development:
Not an easy task, but solvable. The project was started under this motto and after a short time RadioForce was able to present a solution that was then confirmed in a POC (Proof of Concept) together with the OEM.
New specifications and problems! ... and no end in sight.
The next step was real production. The conditions there are a bit more demanding. An additional problem was that there were a total of 14 different installation positions and there was a production requirement of achieving a readability of 98.5%. Last but not least, all of this should be done on 8 different vehicles!
These new, additional parameters were included in finding a solution. By far one of the most complex and demanding projects that RadioForce has been approached to date.
Ultimately, RadioForce was able to work through all the issues and offer solutions. Thanks to the very cooperative and constructive cooperation with the OEM, EVERYONE could be satisfied. After working through the various topics, the RadioForce achieved a reading ability of originally 85 - 86% and after implementing all solutions a reading ability of 99+% (partially 100%).
This project has been running sustainably since November 2021 until today! An RFID solution at the ASÖ has now been expanded to 3 plants and more are to come.
A project to our liking. It requires thinking outside the box while remaining focused on finding solutions.
We would like to thank everyone involved for the cooperation.
On to the next challenge to the RadioForce RFID Solutions Team....
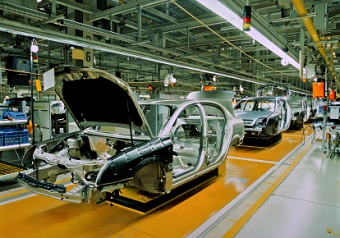